Industrial Manufacturing
Model new manufacturing processes prior to implementation or existing ones in order to diagnose problems. Use Mathematica for analyses including pre- and post-processing of models, simulations, and results.
Connecting Systems with OPC
The OPC Classic Library allows you to connect your simulation models to the real world using Open Platform Communication (OPC). Here, we will connect a process plant model and a real-world Programmable Logic Controller (PLC) in System Modeler to allow them to communicate with each other through OPC.
Accessing Production Data
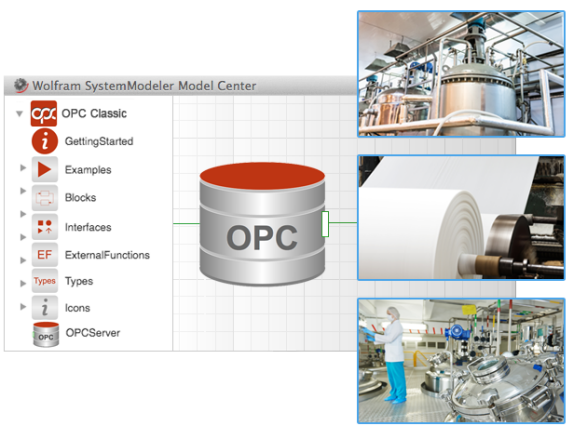
With the OPC Classic Library in System Modeler, it is possible to link your simulation models to the real world by connecting to OPC servers.
In this case, the OPC Classic library is used to test a new design of a PLC before it is connected to the real process plant. A model of the process plant has been created in System Modeler, and the PLC can communicate with the model through the OPC interface.
Data from the process plant model is written from System Modeler to the OPC server, and is then read by the external PLC. The PLC computes a control signal that is written back to the server, from where the process plant in System Modeler can access it. Check out the video below to see how well the PLC manages to control plant behavior.
Simulate the model in real time and plot the production rate of the machinery and the reference signal. From the plot, we can see that the PLC can control the machinery reasonably well, but might need some additional tuning to decrease the initial oscillations.
Exchanging Data with OPC Classic
When modeling with OPC Classic, you have control over how data should be read from or written to the server. It is possible to choose from a variety of settings, such as sampling rate, when sampling should start, how often the server should update, and if you want to sample regularly or irregularly.
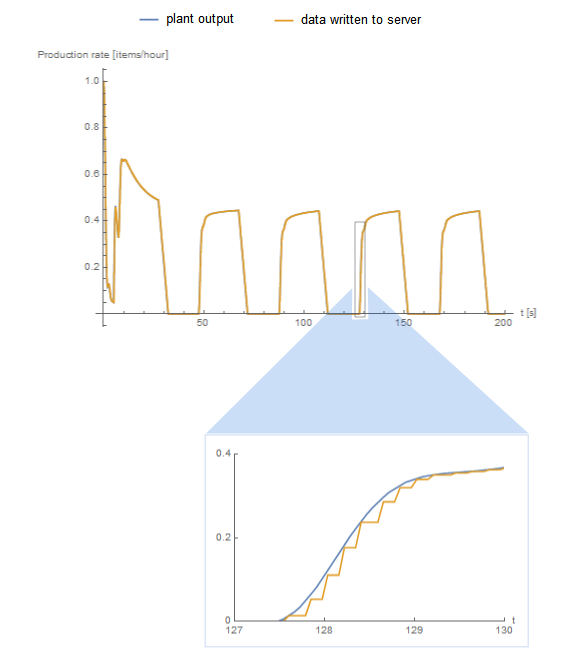
The output from the plant is sampled regularly every 0.2 seconds, and then written to the server.
This example shows how to use OPC Classic and System Modeler to verify the design of a process plant PLC. Using the same principles, it is also possible to do state estimation, data monitoring, data analysis, simulate test benches, and more.
Wolfram System Modeler
Try
Buy
System Modeler is available in English
and Japanese
on Windows, macOS & Linux »
Questions? Comments? Contact a Wolfram expert »