機械工学
SystemModelerを使うと,運動学的挙動,動的挙動,熱挙動を伴うメカニズムや機械を含む動力学問題をモデル化し,シミュレーションを実行することができます.振動問題を調べ,解決します.
Asynchronous Induction Motor with Slip‐Ring Rotor
When starting industrial induction motors, different methods are often employed to prevent damages to the motor windings due to high starting currents. Here, we study how the use of rotor slip rings connected to a rheostat—an adjustable resistor—can be used as one such method.
The AIMS Model
For our analysis, we are using the asynchronous induction machine with slip rings (AIMS) model defined in the Modelica.Electrical.Machines library. The slip rings—which allow for the connection of rotating and stationary electrical devices—are connected to the rheostat, which is shortened shortly after the motor has picked up speed. The simulation of the model is compared to that of an asynchronous squirrel cage induction motor (AIMC), a type of induction motor that does not use slip rings.
Simulation Results
As can be seen in the plots below, the current is much lower when using an AIMS. This behavior is explained by the added resistance to the rotor circuit, which reduces both the rotor and stator currents.
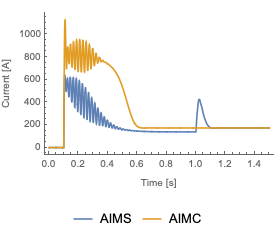
The current drawn when starting the two motors.

Motor speed. Once the rheostat has been shortened, the AIMS reaches its nominal speed.
Wolfram System Modeler
評価版
ご購入
System ModelerはWindows,macOS,
Linuxで
日本語と英語でご利用になれます »
ご質問やコメントはWolframエキスパートまでお寄せください »